
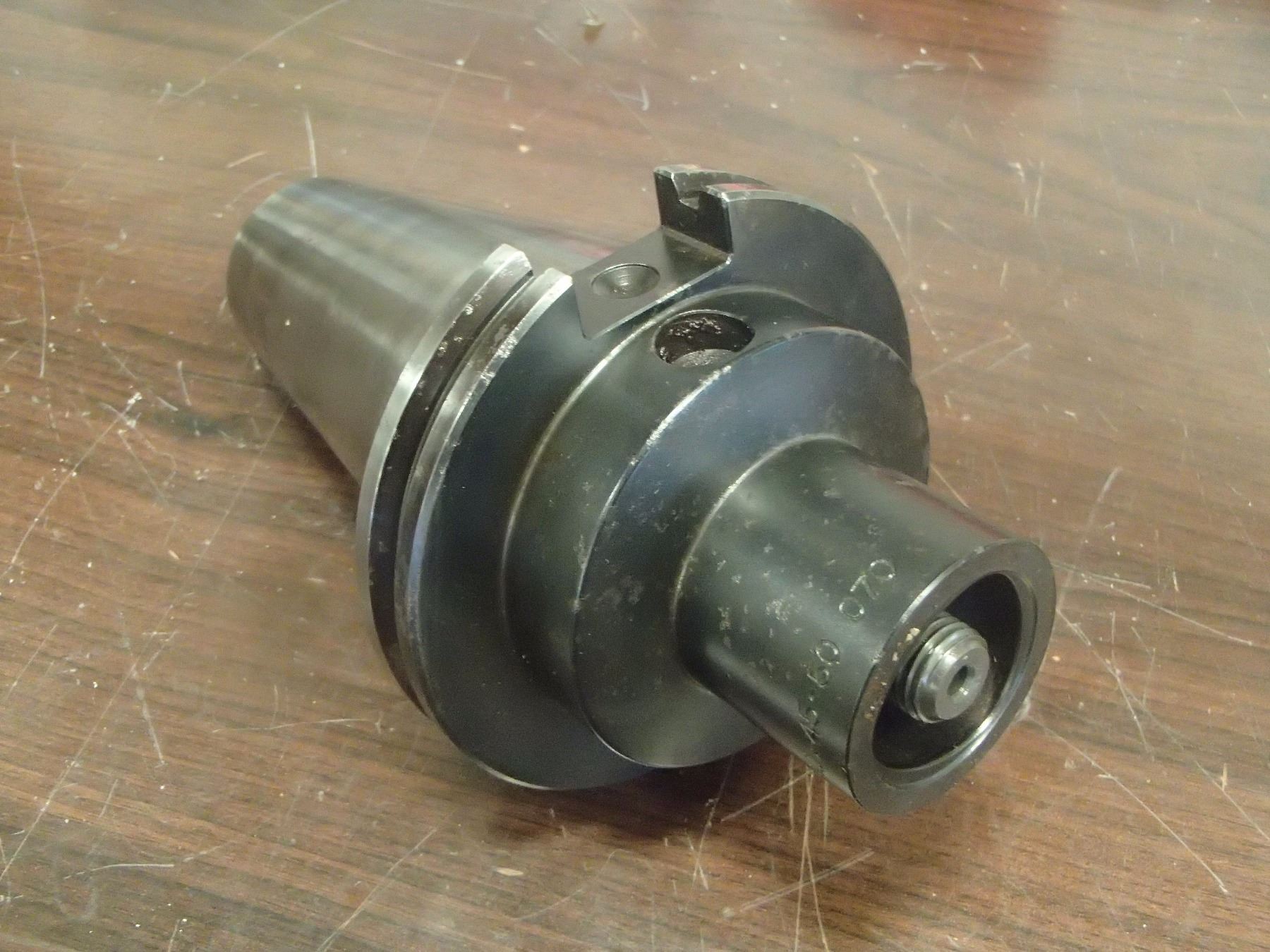
Conversely, a holder meant for rough machining usually will lack balance qualities that would allow it to run smoothly at high speeds in finishing operations. A tool holder engineered to carry out high-speed finishing operations typically will lack the rigidity and strength needed to be effective in, for instance, deep roughing of raw castings. No one tool holding method is appropriate for all possible applications. Nevertheless, while shops seek to acquire the most advanced machine technology and cutting tool materials, they often place minimal importance on selecting, applying and maintaining tool holders that best fit their specific production needs. A machining shop, therefore, should base its choice of tool holders on its specific operations as well as on the parts it produces.
#CAPTO TOOL HOLDERS USED MANUAL#
Coolant supply via external docking point – either automatic or manual.Automatic, quick tool change, either from the tool magazine, pick-up magazine or prismatic tool changer.High coolant flow rate for large hole diameter.High coolant pressure for small hole diameter.Supply option for the right coolant pressure and volume:.Deep hole drilling: gun drilling, ejector drilling, HTS drilling, etc.WFL prismatic tools for deep hole drilling

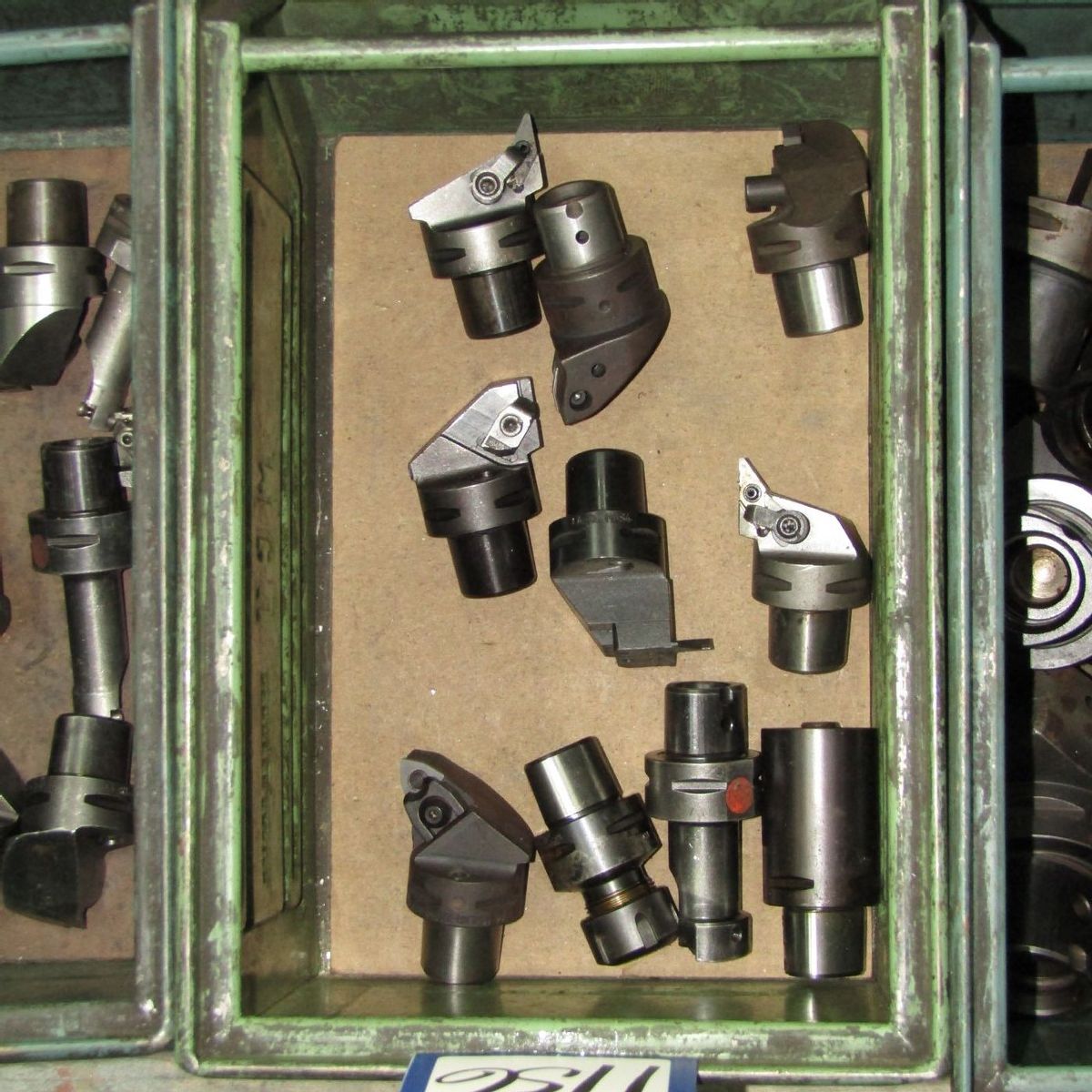
Boring bar overhang up to 18xD already achievedĢ.Perfect clamping results for optimum machining with maximum boring bar overhang.Vibration damped, carbide-reinforced boring bars Cost-effective variant for use of different cutting heads or use of sister tools during extensive internal machining.The same HSK or Capto tool system as in the turning-boring-milling unit.Fully automatic tool change on a stable and optionally vibration damped basic boring bar.Optimum stability conditions during tricky internal machining.WFL prismatic tools for internal turning operations Suitably equipped tools provide information on utilisation, temperature, deflection, and the surface quality achieved and actively intervene in the machining process in the event of an overload.ġ. The machine can respond interactively to a defined trigger event. Integration of ultra-modern sensors enables detailed tool information and machining states to be called up on the controller or tablet.
#CAPTO TOOL HOLDERS USED FULL#
These tool solutions enable users to maximise the machine‘s full potential. WFL prismatic tool holders can be used for precisely this kind of challenging machining operation and are secured to the turning-boring-milling unit in addition to the HSK or Capto tool system with a prismatic tool accommodation. Hard to access machining area often require long special tools. WFL develops special tools which are perfectly tailored to the MILLTURN and are used to machine complex workpieces.
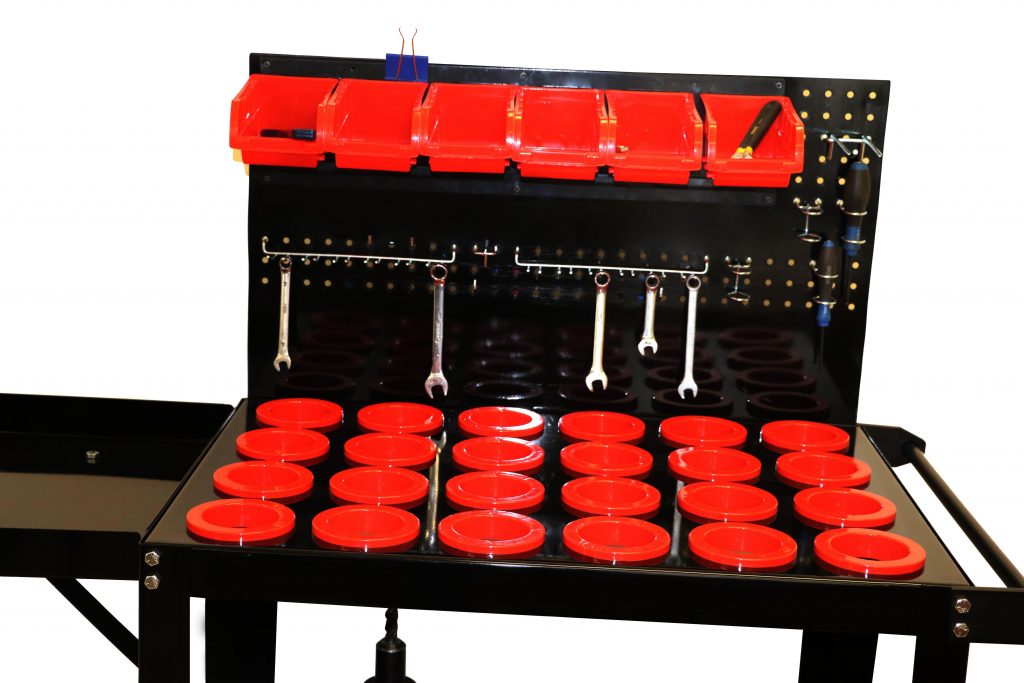
Increase in performance for the turning-boring-milling processes thanks to WFL prismatic tools
